The Internet of Things (IoT) technology has evolved, creating a real-time data warehouse, and the analysis of that data warehouse has made major changes in manufacturing activities. Decisions based on “real-time data” are an approach in smart manufacturing that optimizes all activities, such as sales and production planning, productivity enhancement, supply chain optimization, and better delivery of after-sales services.
Benefits of using data for smart manufacturing
- Enhanced information visibility: Company leaders and the manufacturing sector can monitor the operation of the entire manufacture in real-time. Based on this accurate information, the operator can measure the performance of each stage of production, precisely and in detail what is happening, identify flaws from which to make decisions to adjust operations and processes, and measure the effectiveness of these changes.
- Optimize operations and reduce futile costs: With large datasets collected from devices and applications, manufacturers can use AI algorithms that help solve complex problems. For example, an automaker may use accumulated customer orders to better forecast future demand, adjust material orders, and allocate warehouse space in line with production and inventory. In addition, based on the operational history and maintenance information of machinery, AI technology can predict possible damage to the equipment and give proactive maintenance schedule suggestions following the production plan. This minimizes the possibility of devices suddenly shutting down, affecting production lines.
- Automation: Data and IT technologies developed such as IoT technology, image recognition using AI technology,… created new automated lines without human intervention. For example, in the production line, by using a combination of cameras and AI image recognition technology, the line can automatically detect defective products and use robotic hands to remove such products, while adequate ones keep running on the line.
- Developing customer-centric production methods: By collecting and analyzing information related to customers’ needs, preferences and habits instead of traditional mass-production methods, enterprises can design and produce separate products for each target group, shorten the time it takes to launch new products or allow users to directly order and produce on demand.
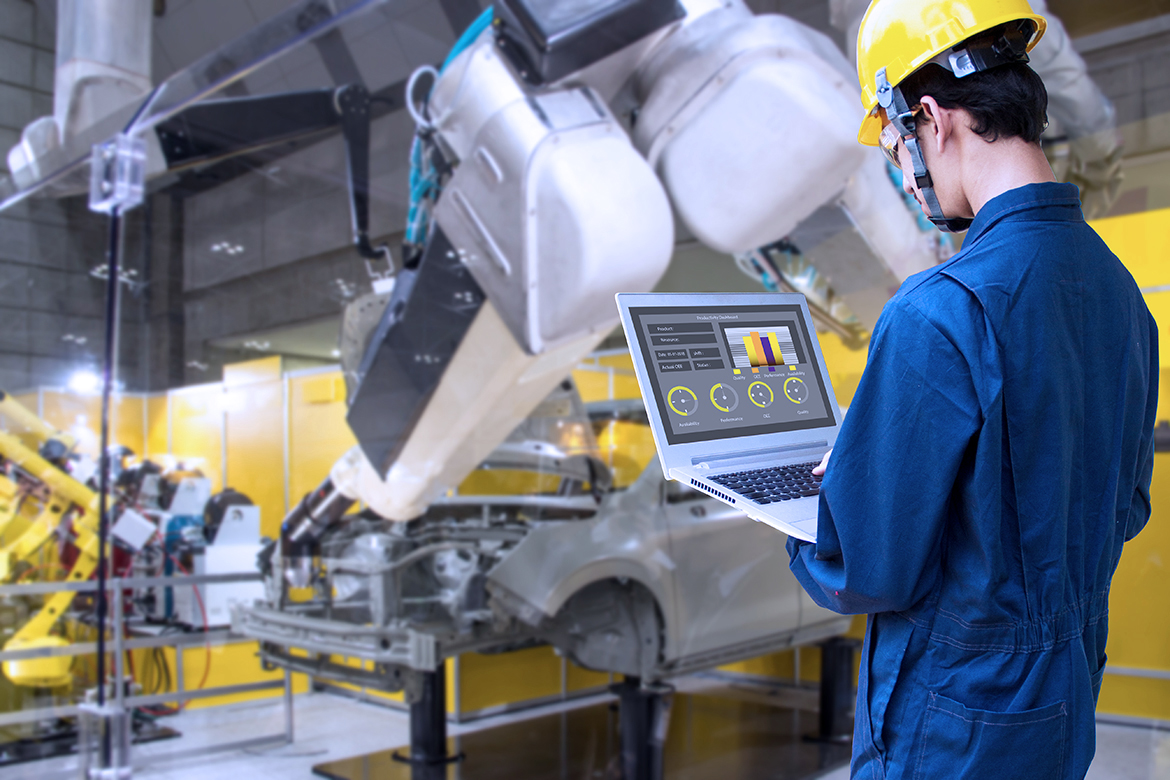
The challenges of smart manufacturing using data
- Individual systems and data dispersion: Smart manufacturing needs the analysis of data from a variety of systems and data sources such as production databases, control systems, ERP systems, and MRPs (Resource Planning Processes). However, most of these systems are individual systems, so businesses have a lot of difficulties collecting and integrating data from these systems.
- Outdated systems and equipment: Many outdated systems and equipment were not originally designed and built to exchange data with one another. So it can cost businesses a lot to build more IoT tools and devices that help collect this data.
- Security threats: Industrial IoT security issues have arisen for two main reasons. First of all, because the more devices are connected, the more likely it is to create security vulnerabilities for new devices. Secondly, the security of devices has not been noticed before, so the engineers operating the device system also have little security experience and are vulnerable to being attacked.
Most read article
Intellectual property in Vietnam: the status of protection and exploitation of intellectual property
Digital Strategy 07/03/2022
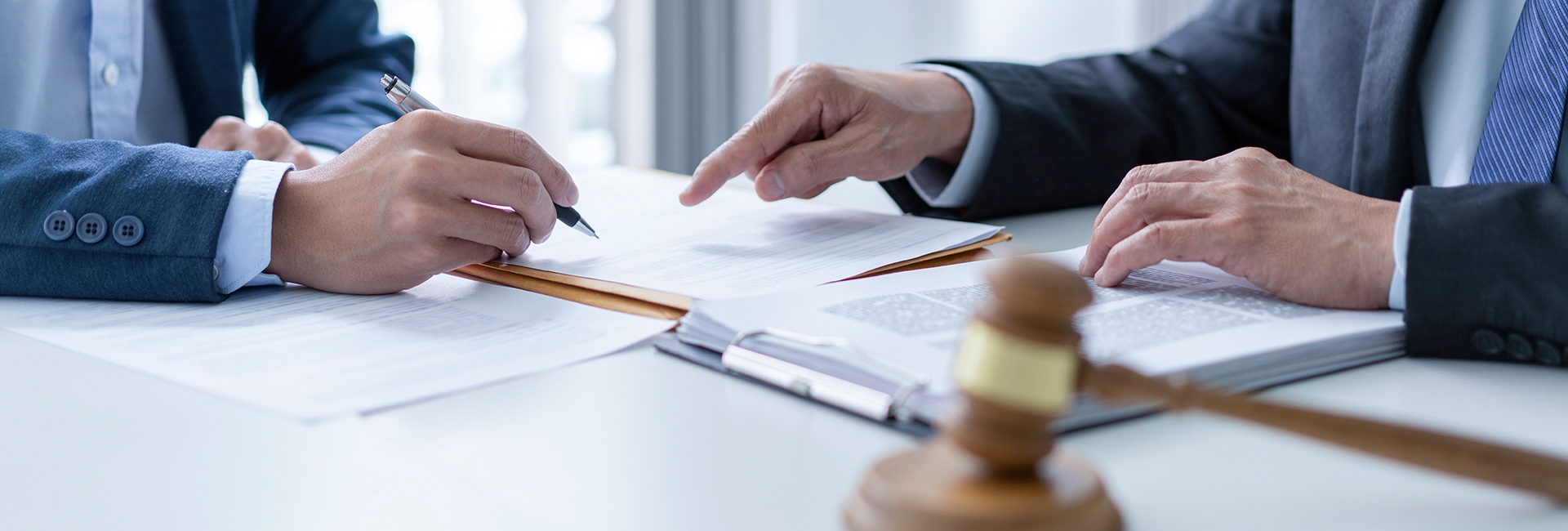
Strategy of using data usage to support smart manufacturing
To implement data initiatives that support smart manufacturing, the company needs to develop the right strategy and be ready for radical organizational and technological changes. These changes focus on the following points:
- Develop a data utilization strategy and analysis along with a specific implementation roadmap: Businesses build a distinct future scenario of the use of data that shapes smart manufacturing and pathways to achieve goals. This makes it possible for the company to allocate investments reasonably and track results in each stage of development. Moreover, with a clear future vision, an easy-to-understand roadmap, and sharing of the benefits of data will facilitate management and employees to collectively support the implementation of the strategy.
- Digital capability building: To create and improve digital initiatives using and analyzing data, businesses need to build digital competencies that are a combination of technical skills and specialized industry knowledge. For example, an application that forecasts material demand needs to be coordinated by AI engineers, data engineers, and managers, employees who are knowledgeable about manufacturing and planning. However, building a team of technology experts for manufacturing enterprises, especially in the context of Vietnam, is a difficult task due to the lack of expertise and funding to maintain a specialist team. Therefore, businesses can look for experienced technology partners to do digital transformation, in order to support the implementation of these projects.
- Build a data collection, storage, and analysis platform: Data often exists in multiple systems of different departments. The combination and correlation of this inter-departmental data will help businesses discover new values of data and thereby optimize production and business activities. Therefore, the general data collection, storage, and analysis platform will create a favorable environment for businesses to quickly build data equations and use those data to support important decision-making.
- Ensuring data security: Along with exponential increase in value, data has become a valuable asset of the business. If data is leaked, the business will lose not only credibility, technological secrecy, competitive advantage, but also the cost of solving these problems. Therefore, businesses need to equip security solutions and experts to minimize the vulnerabilities of devices and applications, as well as data security awareness training for all employees at all levels.
Implementing the priorities mentioned above will help businesses make breakthrough changes in improving productivity, optimizing operations, and providing refined products & services that better serve customers. In order to avoid errors in the process of developing and implementing strategies, enterprises need to invest their resources and coordinate with experienced partners in the field of digital transformation to assess the current status and maturity of enterprises on the application of data in smart manufacturing; and building the future vision, strategies, and roadmaps for implementing initiatives to quickly achieve these goals.