The COVID-19 pandemic has made a significant impact on the manufacturing industry by creating disruptions across the entire supply chain. Manufacturing enterprises need to quickly adapt to these changes and follow major future trends to ensure success in business development.
Even before the COVID-19 pandemic changed the global economy, manufacturing companies encountered many problems in their operation strategies. The outstanding development of technology has prompted significant investment in digital transformation, especially when businesses realize the difficulties in improving labor productivity and maintaining and replacing old assets.
As the COVID-19 pandemic broke out in waves, the need to transform digitally became even more urgent. Faced with sudden changes such as stagnation in local business activities, supply chain disruptions, and the backlog of goods in production, manufacturing enterprises began to see the advantages of how digital initiatives related to smart factories would help address these pressing needs.
In addition, production and logistics operations have been disrupted globally, leaving many businesses grappling with uncertain delivery times and severe shortages of parts and materials. Hence, what strategies should manufacturing enterprises devise to cope with these disruptions?
3 Major development trends
To solve the problems caused by the pandemic, manufacturing companies around the world have researched, tested solutions, and come up with three major development trends to implement, which focus on:
- Sustainable manufacturing: Promoting sustainable supply chain integration with improved internal efficiency through waste-reducing, environmentally-friendly manufacturing that enhances the ability to resist business environment changes.
- Using the ecosystem to promote the development of smart manufacturing: Strengthening the development capacity to extend to the ecosystem outside the enterprise.
- Focusing on human resource development: Improving human development capacity, creating a foundation for future development.
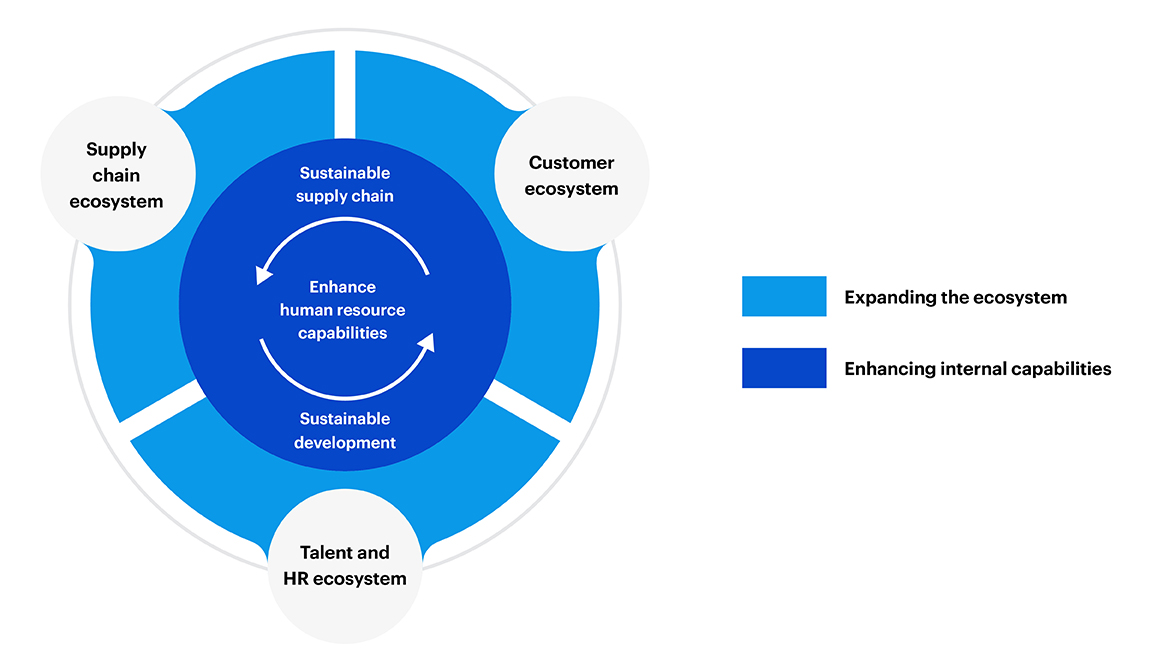
Sustainable production
Sustainable production needs to focus on controlling raw materials sources and production outputs to ensure that factories are always operating under suitable development conditions. In addition, sustainable production also aims to integrate issues related to product designs and processes including production, planning, quantification, evaluation, and management of waste flows into the environment.
The ultimate goal of this activity is to minimize the impact on the environment while maximizing the efficient use of resources (5). This goal can mainly be achieved through the application of best practices related to product design, process design, and new operating principles that affect the entire range of existing processes and is assessed as bringing outstanding change to the business (2)(6).
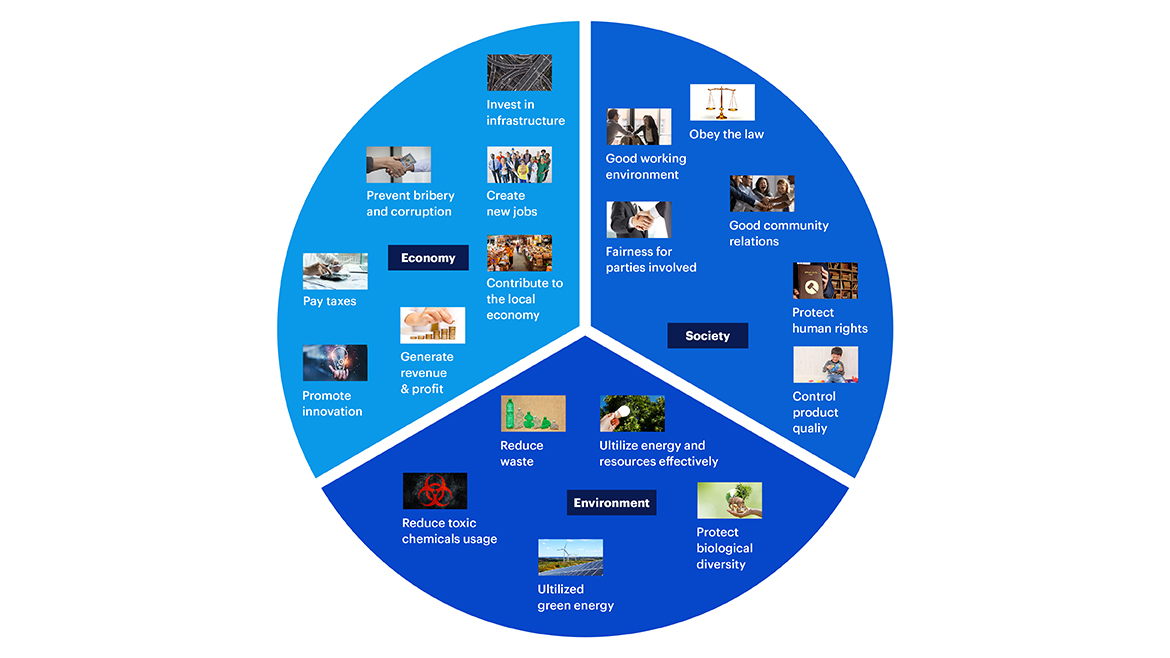
Using the ecosystem to promote the development of smart manufacturing
Creating an ecosystem for smart manufacturing is not simple. Many factors can hinder enterprises’ efforts to connect with the overall ecosystem to promote alignments in the field of smart manufacturing, such as difficulties in data coordination and protection, network security, intellectual property theft, constantly changing skills needed, and synchronization across departments in the business (1)(3).
Indeed, the ecosystem is not only defined as a relationship with a supplier, or a relationship with a seller but much broader and can be defined in terms of key aspects such as:
- Internal Ecosystem: Involving day-to-day operations within the factory to help create products that meet customer requirements with consistent quality standards and effective cost margins.
- Supply Chain Ecosystem: Expanding beyond the factory and including input materials sourcing, supply-demand alignment, storage facilitation, and finished products distribution to customers.
- Customer Ecosystem: Activities connected with a subset of the customer ecosystem, which can differentiate channel partners in the way people use social media helps to connect and interact with customers, allowing customers to order, maintain, and service products.
- Talent and HR ecosystem: Linking all three above ecosystems; focuses on how organizations can attract talent, and build the right human resources to target the required roles and the right career paths to support smart manufacturing.
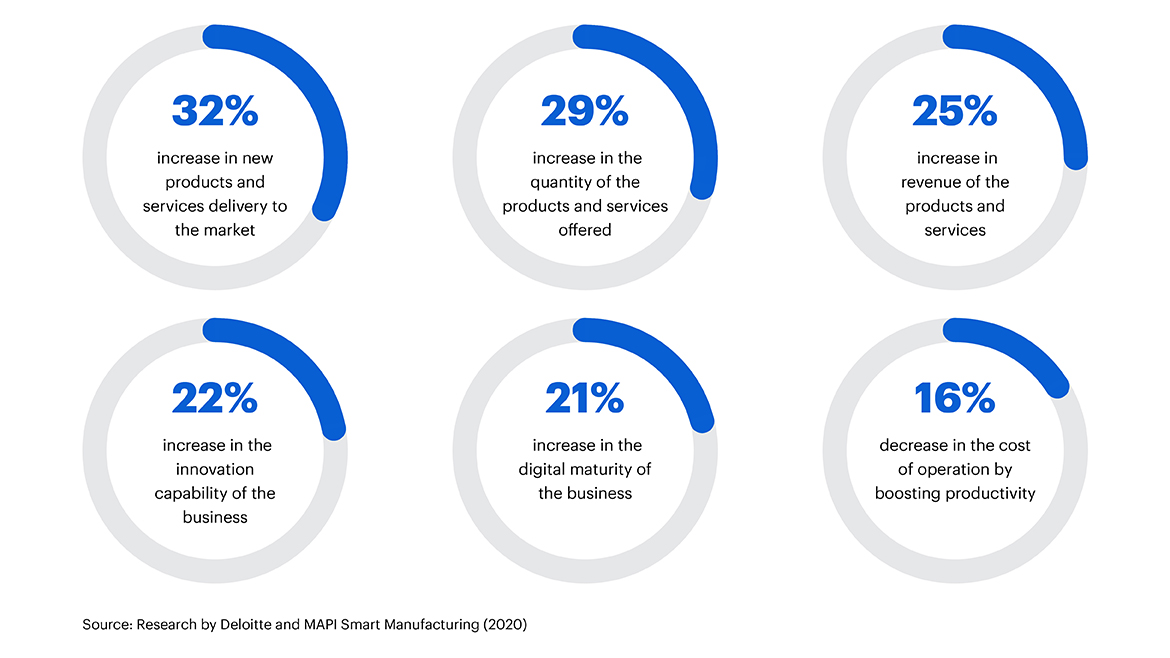
Case study: Schneider Electric started its Digital Transformation journey many years ago, in which they developed a series of smart manufacturing systems based on digital technology and used an ecosystem approach to overcome global disruptions. They started by working with 5G and AI providers to develop application tools for those in their ecosystem.
In addition, Schneider promoted the expansion of digital tools to improve supply chain transparency and coordinated with local partners to minimize disruptions from overseas suppliers. All of these actions helped to improve flexibility and shorten the time to support production and business operations.
Focus on human resource development
The development and application of disruptive technologies is an important step in driving the growth of smart manufacturing, but the platform alone is not enough for deep integration between parties involved in the supply chain and ecosystem.
Creating strong and sustainable cooperation requires more supporting factors to achieve desired results; in which businesses tend to focus on the human resource development factor as it lay out a foundation for development and success in the future (3)(4).
In contrast to the opinion that machines will replace humans in production and operation activities, industry 4.0 creates a lot of new jobs. The main changes will focus on the tasks that workers take on. This means that increased automation is not intended to replace existing jobs, but to redefine and change the skills and abilities that workers need to perform them.
The future of work requires major changes in the workforce:
- Upgrading: Employees need to gain new skills for their current roles.
- Re–skilling: Employees need to develop enough capabilities to take on different or entirely new roles.
The challenge of re-skilling will be especially difficult in the operationally intensive sector such as manufacturing (or shipping, retail, etc.), where the change should be implemented smoothly, without affecting the daily work.
These businesses will have to experience greater variability than the global average because of their heavy use of human resources and the nature of their jobs with many repetitive operational tasks, which are suitable for automation and digitization.
The fourth industrial revolution in Vietnam is being promoted strongly due to the impact of the COVID-19 epidemic. As the global business environment cannot be stabilized quickly, this situation urges manufacturing companies to strengthen their capacity in Digital Transformation to create a breakthrough in labor productivity, accelerate new product delivery to market, and create new markets that focus on sustainability.
Many manufacturing businesses choose to use a growth strategy through the adoption of disruptive technologies that are setting new standards in the industry. Therefore, businesses that are behind, or not digitally ready in this period will be surpassed by their competitors in the increasingly competitive future.
Reference sources:
(1) Deloitte. 2020 Accelerating smart manufacturing.
(2) OECD. About sustainable manufacturing and the toolkit.
(3) McKinsey. Manufacturing reimagined: from improved productivity to profitable growth.
(4) McKinsey. 2020 Building the vital skills for the future of work in operations.
(5) Manufacturing Management. 2021 Efficiency, not sustainability, top of UK manufacturing’s esg priorities PwC finds.
(6) Foundry. Six Key Factors for Achieving Sustainable Manufacturing.