One of the biggest values, and also the biggest challenge of Lean manufacturing is continuously detecting wastes and continuously improving and fixing them. This means there is no limit of efficiency in lean production, and everything can be changed and get better day by day.
For businesses that have been operating for decades, all activities seem to have come close to perfection in the production and coordination processes, and it is difficult to find gaps to change. The arrival of the 4th industrial revolution and the wave of Digital Transformation, however, has changed that. Lean manufacturing can turn a new page with digital technology.
Digital Lean – Lean in the digital production environment
If you’ve ever heard about Lean, you’ll probably be very familiar with the 8 wasted factors (7 factors according to the original Taiichi Ohno and 1 factor added by researchers later). These 8 factors are considered as goals for Lean to target and find solutions to improve business efficiency. To get acquainted with these terms easily, the initials of these eight factors are combined into the word DOWNTIME as a warning for operators about the problem of wasted production. Those factors are:
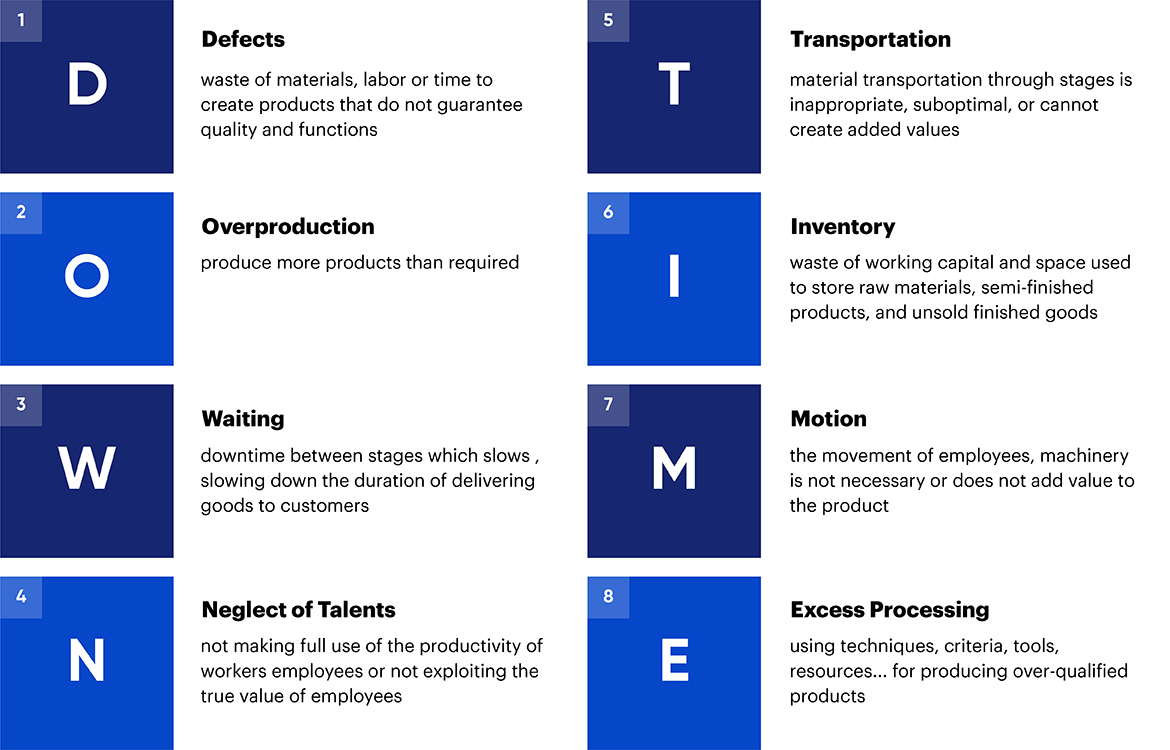
Normally, to detect waste factors, production operators need to undergo actual observations in the workshop and analyze statistical data. Before digital technology, these activities were relatively difficult, and they required a lot of lean
manufacturing knowledge and experience. This itself creates an obstacle that it was difficult to apply Lean on a large scale in the organization, causing bottlenecks – an issue that goes against the Lean principle.
The development of digital technology seems to have solved this bottleneck quite effectively. With the participation of new technologies such as automation, IoT, big data, AI, etc., production information is collected comprehensively, which creates a panorama for operators.
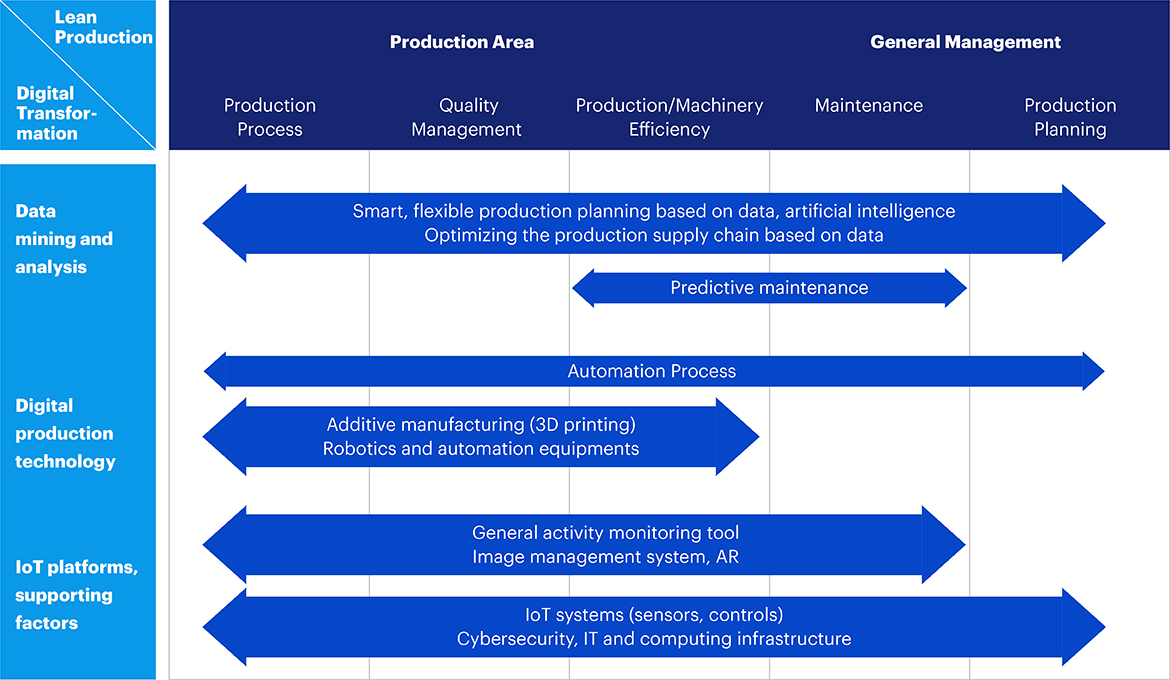
Applying digital technology, the entire production picture will be digitized and proceed to form a digital twin. The production executive can now visualize the entire production process: Identify the problem that happened in the production area, its causes and quickly find a solution to ensure seamless production.
At a higher level, with automation technology adoption, many production processes will be controlled automatically based on the actual status between stages. The production stages are linked, machines will communicate between each other to ensure that the semi-finished products are delivered at the right time, in the right quantity and the number of residual semi-finished products on the line is minimized.
Finally, when the entire production system is operated in a digital environment, data from production areas will be mined and analyzed to build a complete picture of the production value chain. Actions to optimize the plan, predict production progress will be maximally supported by systems equipped with machine learning and artificial intelligence technology to offer suitable options for production operators to make decisions.
Digital Lean – the good results come from perseverance
Applying digital technology in lean production for factories is not just an overnight success. It requires significant investments in both human and material resources, as well as the perseverance of the entire organization especially the leadership to draw up a long-term strategy for the business.
The first obstacle that most businesses face is how to combine information technology (IT) systems and operational technology (OT) systems. The integration between IT and OT plays a critical role in the ability to collect and share data between the two operating departments, thereby maximizing the potential of production activities.
On the other hand, having too much data is also a challenge for manufacturing enterprises. Which data can make decisions, which data is only supplementary, etc. all need to be analyzed and agreed upon by the parties so that effective data flows can be established.
Ultimately, the transition from traditional lean to digital lean requires embarking on practical actions. These actions need to follow a common vision and reach consensus throughout the organization, from the leadership to the workers who are directly operating. The transformation will be difficult to reach the destination and achieve sustainable effectiveness if there is a lack of unity in vision and action plan.
Behind all the above difficulties, lean production in the digital environment promises to bring significant benefits to factories. A study by Bain & Company shows that applying digital lean manufacturing can help businesses reduce production costs by up to 30% – compared with 15% if only applying traditional lean production (2). Another study by Deloitte also shows that digital lean manufacturing improves overall equipment efficiency by 10% – 30% and improves safety and sustainability in production by 3% – 10% (1).
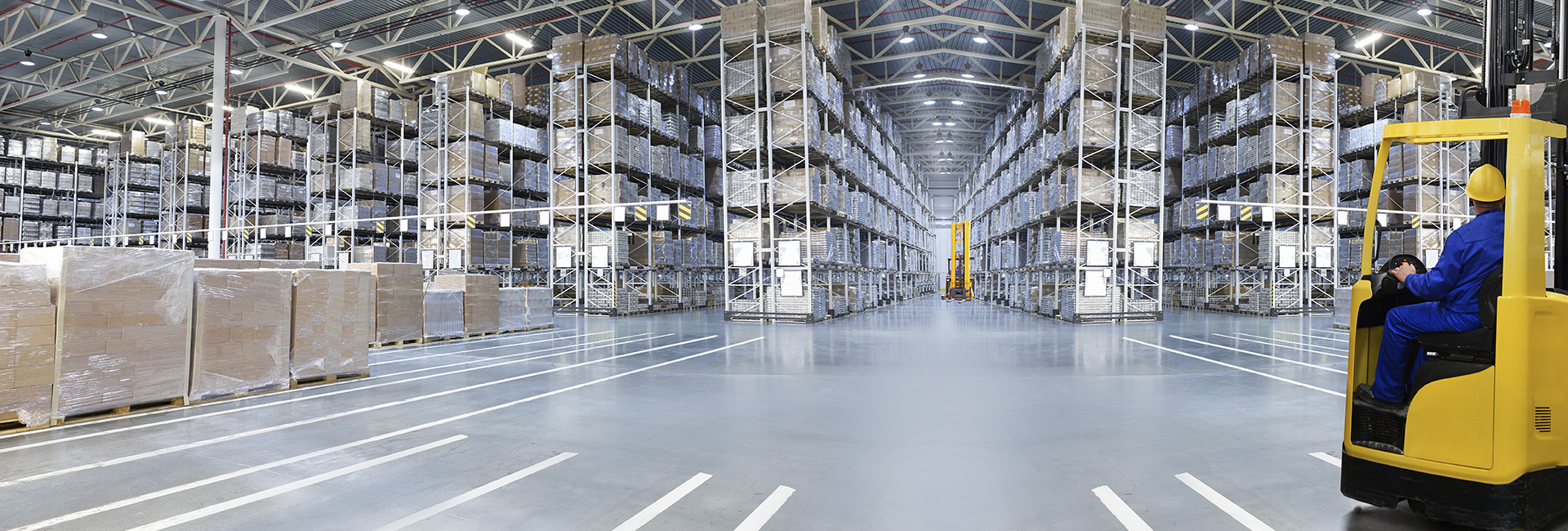
Case Study: Siemens’ Digital Lean Factory
Since 2017, Siemens has started building its digital lean factory program. The program has brought together 140 leading experts from more than 30 Siemens factories and partners to design the architecture of the new generation of Siemens digital factory. More than 40 initiatives have been developed focusing on three directions: cost reduction, scalability and flexibility. These initiatives help Siemens improve productivity by 7%/year while reducing production costs by 20% (3). At the same time, these initiatives help Siemens maintain innovation and continuous improvement within the organization, thereby maintaining its leading position in the digital manufacturing industry.
Reference sources:
1. Deloitte. Industry 4.0 technologies transform lean processes to advance the enterprise
2. Bain & Company. Digital lean: a guide to manufacturing excellence
3. The future factory. Siemens Case Study: Lean Digital Factory Project